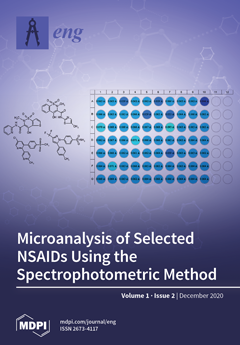
Advances in Engineering
Yazarlar: -
Konular:-
DOI:10.3390/eng3010002
Anahtar Kelimeler:Additive manufacturing,3D printing,Fused deposition modeling (FDM),Material extrusion additive manufacturing (MEAM),Fused filament fabrication (FFF),Finite element method (FEM),Poly-ε-Caprolactone (PCL),Lattice structures,Scaffolds,Orthosis
Özet: Material extrusion additive manufacturing (MEAM) is an advanced manufacturing method that produces parts via layer-wise addition of material. The potential of MEAM to prototype lattice structures is remarkable, but restrictions imposed by manufacturing processes lead to practical limits on the form and dimension of structures that can be produced. For this reason, such structures are mainly manufactured by selective laser melting. Here, the capabilities of fused filament fabrication (FFF) to produce custom-made lattice structures are explored by combining the 3D printing process, including computer-aided design (CAD), with the finite element method (FEM). First, we generated four types of 3D CAD scaffold models with different geometries (reticular, triangular, hexagonal, and wavy microstructures) and tunable unit cell sizes (1–5 mm), and then, we printed them using two nozzle diameters (i.e., 0.4 and 0.8 mm) in order to assess the printability limitation. The mechanical behavior of the above-mentioned lattice scaffolds was studied using FEM, combining compressive modulus (linear and nonlinear) and shear modulus. Using this approach, it was possible to print functional 3D polymer lattice structures with some discrepancies between nozzle diameters, which allowed us to elucidate critical parameters of printing in order to obtain printed that lattices (1) fully comply with FFF guidelines, (2) are capable of bearing different compressive loads, (3) possess tunable porosity, and (3) overcome surface quality and accuracy issues. In addition, these findings allowed us to develop 3D printed wrist brace orthosis made up of lattice structures, minimally invasive (4 mm of thick), lightweight (<20 g), and breathable (porosity >80%), to be used for the rehabilitation of patients with neuromuscular disease, rheumatoid arthritis, and beyond. Altogether, our findings addressed multiple challenges associated with the development of polymeric lattice scaffolds with FFF, offering a new tool for designing specific devices with tunable mechanical behavior and porosity.