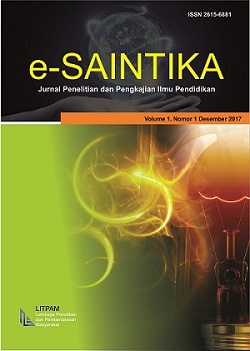
Jurnal Penelitian dan Pengkajian Ilmu Pendidikan: e-Saintika
Yazarlar: Sukainil Ahzan, Darminto Darminto, Ferry Anggoro Ardy Nugroho, Saiful Prayogi
Konular:-
DOI:10.36312/esaintika.v5i2.506
Anahtar Kelimeler:Synthesis,Characterization,ZnO thin layer,Sol,El spin coating
Özet: The potential of thin layer in many applications has led to research on the development of many new materials and their fabrication methods. This study aimed to synthesize a thin layer of ZnO using the facile and low-cost sol-gel spin coating method. The ZnO thin layer is deposited on a glass substrate and analyzed to observe the influence of the deposition variables such as heating and rotation speed, and its aging. The characterization methods include the identification of the formed phase using X-Ray Diffractometer (XRD), and the microstructure and elemental composition using Scanning Electron Microscopy (SEM) coupled with EDS (Energy Dispersive Spectrometer). The study shows that a thin layer of ZnO is successfully deposited on a glass substrate by heat treatment at temperatures of 300 oC and 500 oC. Furthermore, XRD reveals that higher heating temperatures result in higher diffraction peak intensity. At a heating temperature of 300 °C crystals are formed but are not yet perfectly oriented, while they are at 500 °C. On the other hand, higher spin coating rotation speed gives rise to lower intensity of diffraction peak. The ZnO crystallization is easier to form in the coating process with a lower rotation (1500 rpm). Interestingly, the thin layer is stable over time where there is no significant change in each sample, both in terms of intensity and width of the ZnO crystal peak. The results indicate that gel precursor aged less than two days can form ZnO crystals. Finally, SEM results show that the surface morphology of the ZnO layer heated at 500 oC has an average grain size of 300 nm. Based on the cross-sectional results of SEM shows that the higher the coating rotation speed has resulted the thinner of the ZnO layer, where the thickness of the resulting layer is on order >5 mm.