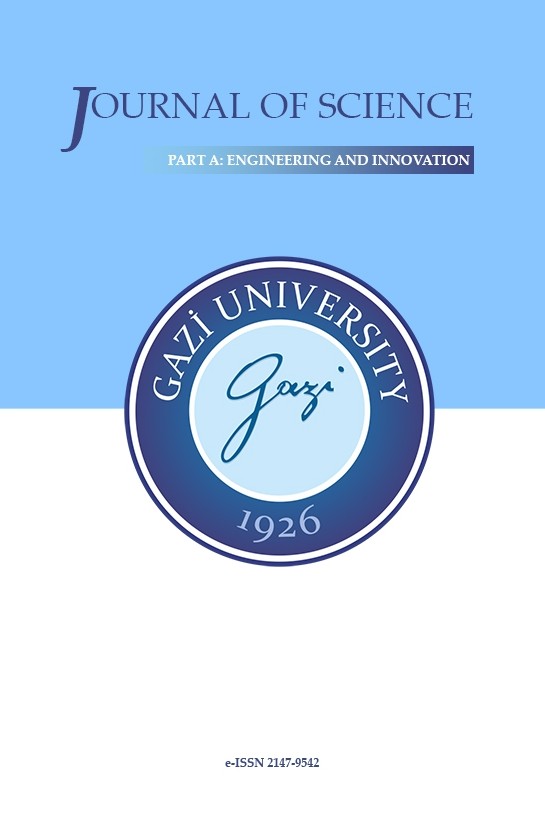
Gazi University Journal of Science Part A: Engineering and Innovation
Yazarlar: Ekom ETUK, Emem IKPE, Aniekan IKPE
Konular:Mühendislik, Ortak Disiplinler
Anahtar Kelimeler:Wind Turbine,Spar,Tip Deflection,Von-Mises Stress,Blade Configurations,Aerodynamic Loads
Özet: The kinetics of wind turbine blade operation in a wind field domain is complex, as rotor blades in attempt to overcome the aerodynamic loads (drag and wake) counteracting the motion of the blade undergo deflections due to induced stresses. In this study, blade tip deflections and induced stresses on NACA 4610 horizontal wind turbine airfoil were investigated at different wind speeds for three (3) different blade configurations (hollow with spar, hollow no spar and solid configuration), to determine rotor configuration with optimum service performance. Using QBlade v0.8, aerodynamic load induced stresses were computed for normal and tangential loads at wind speeds of 2, 4, 6 and 8 m/s for three horizontal axis wind turbine rotor blade configurations namely: hollow with spar, hollow no spar and the solid configuration. The blade tip deflections as well as the resultant fatigue stress for both x and z axis at wind speeds of 2, 4 6 and 8 m/s were observed to increase proportionately with the wind speeds. Within a wind speed of 2-8 m/s, tip deflections increased from 5.8203e-03 to 0.2873 mm and 0.5700 to 1.7347 mm on the x and z axis, while the resultant fatigue stresses also increased from 2.77 to 8.19 MPa for the hollow blade configured with spar. The tip deflections also increased from 5.86483e-03 to 0.2971 mm and 0.589 to 1.7900 mm on the x and z axis with resultant fatigue stresses from 2.88 to 8.54 MPa for hollow blade configured with no spar. Similarly for the solid blade configuration at wind speed of 2-8 m/s, the tip deflections increased from 3.530097e-03 to 0.180601 mm and 0.363439 to 1.09563 mm with resultant fatigue stresses also increasing from 1.91 to 5.55 MPa. Maximum von-Mises stresses recorded along the blade radius occurred at the mid-section (1.2 m), and were 5554030, 81898880 and 8536480 Pa for solid, hollow with spar and hollow with no spar. The solid blade configuration produced the lowest blade tip deflections, fatigue stresses and von-Mises stresses, indicating that it has a higher load bearing capacity than hollow blade with spar and hollow blade with no spar.