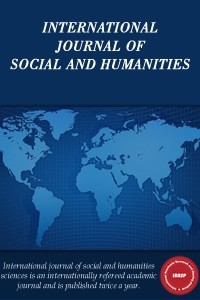
International Journal of Social And Humanities Sciences
Yazarlar: Mahmut TEKİN, Murat ARSLANDERE, Mehmet ETLİOĞLU, Ertuğrul TEKİN
Konular:Sosyoloji
Anahtar Kelimeler:Large-Scale Business,Lean Production,5S
Özet: The rapid development of information communication technologies and the widespread use of the internet have changed the ways and models of doing business in the business as well as changing the way of life of the individu-als. Increasing competition with technological advances, changes in customer profile and increased sensitivity to the environment have led to changes in production and management systems. To be able to provide the products that the customers demand, at the desired time, place and price also requires some changes and optimization of the production systems. In short, it is ai-med to realize flexible production in accordance with customer demands and expectations with minimum resources, minimum wastage, shortest time and minimum cost without any mistakes. when these criteria are met, sustainabi-lity will be achieved. It is the continual improvement of today's businesses to ensure the adapta-tion to changing and developing technology and to be able to respond to customer requests and expectations. Cost savings can only be achieved through continuous improvement which mean lean manufacturing. One of these production applications is 5S. This technique provides many advanta-ges in the removal of unnecessary materials, the stage of regulation and clea-ning, standardization and discipline. With 5S, more effective and efficient work can be done by arranging in the workplaces, preventing unnecessary material stock, increasing employee productivity, performing smooth and easily accessible archiving and reducing waste of materials and labor. The aim of the work is to raise awareness about the full participation of mana-gers and applicability to all processes through the 5S method as a means of lean management and lean production and to ensure that efficient and effici-ent production takes place. As a result, possible applicable 5S working areas were identified and carried out with stages of removal of unnecessary materials, sorting, arrangement and cleaning, standardization and discipline in flour factory. Successful results were obtained in terms of zero excess process loss, zero unnecessary movement and zero labor loss with 5S appli-cations carried out in the areas of transpalet, inventory and forklift parks,
Dergi editörleri editör girişini kullanarak sisteme giriş yapabilirler. Editör girişi için tıklayınız.